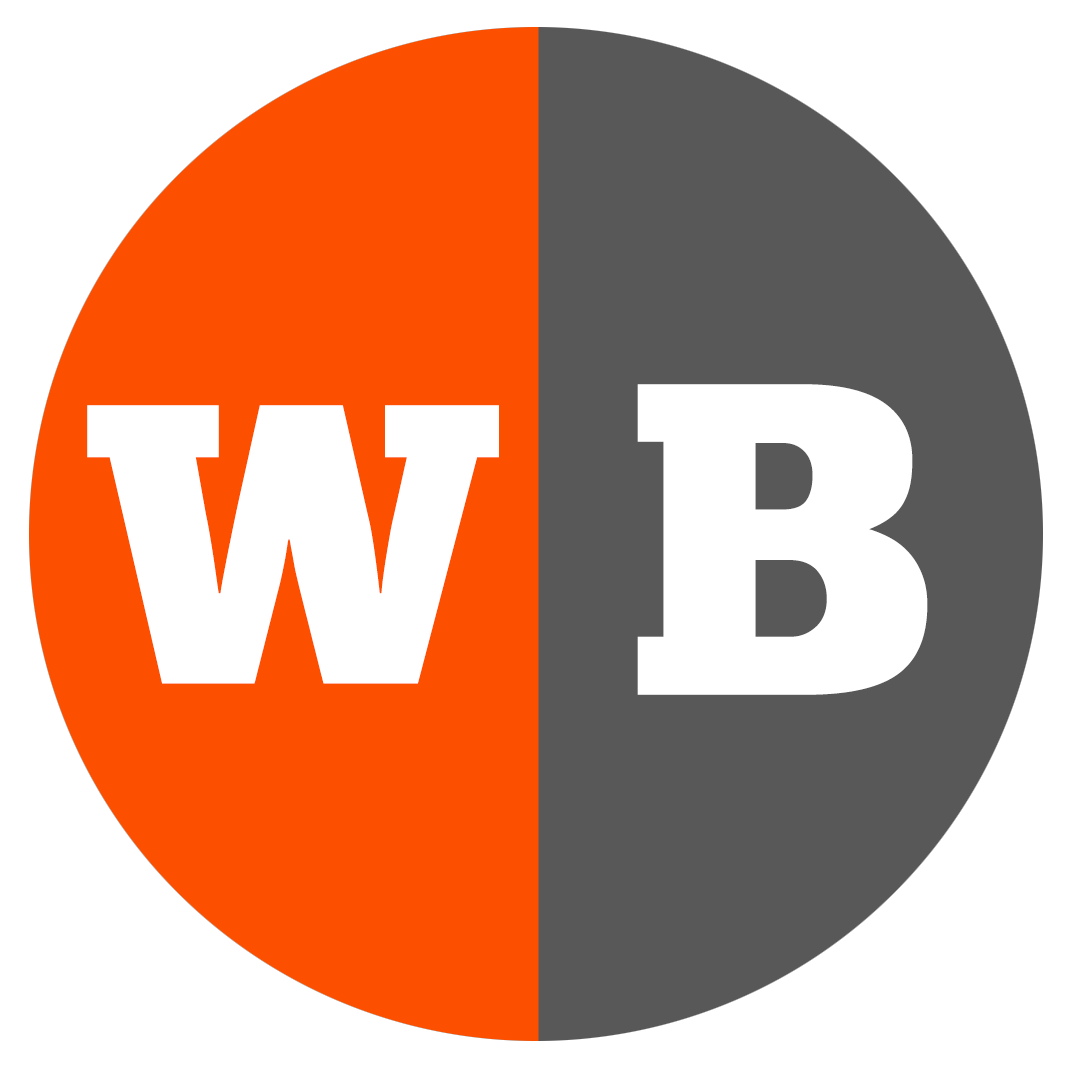
Base-Coat Epoxy Cure:
Ready for protective top-coat: dry to the touch (4-18 hours)
Light Duty Use: 16-30 hours
Full Cure: 5-14 days
This is where the spiked shoes really come into play. Spiked shoes will allow you to walk on the wet epoxy without leaving footprints, damaging the ability of the epoxy to accept the flakes evenly.
Flake Coverage:
(Choose your polyurethane option when ordering.)
We suggest the use of a top-coat to add durability, protection, and to smooth out the flake surface so it isn’t too abrasive. Two layers are typically suggested with any interior project receiving a polyurethane coating, with the second layer applied as soon as first coat can be walked on, and is used in the same manner as the first coat.
STOP: Open the garage doors and inspect the room for adequate air movement and ventilation!
Top-Coat Cure:
Ready for recoat: 6-8 hours
Light Duty Use: 24 hours
Heavy Traffic Ready: 3 days
Full Cure: 5-7 days
Precautions: We do not suggest driving on the epoxy flake floor until at least 5-7 days after application. Always avoid turning your front tires on your new surface as a precaution. Do not slide heavy items as it could tear up the flakes. Use rubber or felt pads for protection under objects and felt pads when sliding large furniture, items, or objects.
© 2025 - WiseBond®, A product of DeckWise®, The Ipe Clip® Fastener Company